Equipment Tracking Features
Equipment management systems are made up of multiple tools that aid in effective equipment tracking, maintenance for construction equipment, equipment utilization, construction safety and more.
In this page you’ll learn the benefits and values of core fleet management features and functionalities including asset tracking, geofences, preventative maintenance, safety and compliance, integrations and many more.
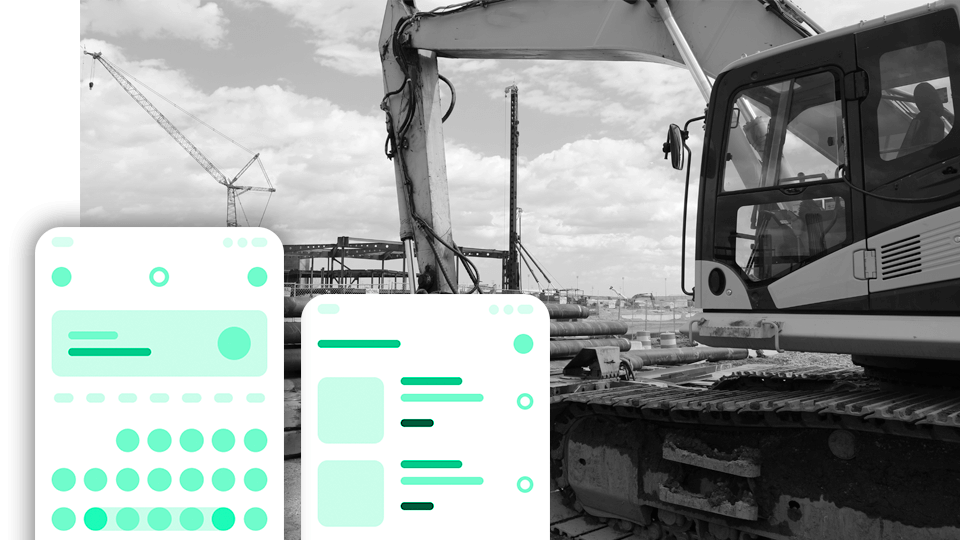
Step away from your desk and maintain visibility by managing your equipment fleet as a whole.
Equipment management systems support assets of every type and size with asset tracking technology for your entire equipment fleet. Manage your assets efficiently and receive valuable insights on your business reliably and accurately so you see the big picture, improve communication, strengthen your operations and grow your bottom line.
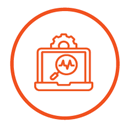
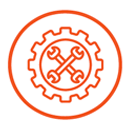
Benefits
- Increased visibility and transparency
- Improved communication between the office, field and shop
- Increased efficiencies and productivity
- Improved decision making
- Reduced wasteful behavior
- Reduced unnecessary costs and increased savings for better margins
With your assets under one roof, you have a central repository for all static and dynamic data pertaining to an asset that your entire organization can source from.
Information on all asset types is stored in your Asset List and can be classified and categorized the way your business does it not for a smooth transition.
Do your assets ever seem to “walk off” your project sites? Do you want to be notified when your assets are moving during off-hours?
We felt the need for this visibility on our job sites, so we understand what you are looking for and deliver it to you across your sites. Create virtual geofences around select areas of your projects, yards and offices to monitor where your equipment fleet assets are.
Benefits
- Increased visibility and improved communication.
- Increased efficiency, recordkeeping and mitigate theft and loss.
- Increased productivity with your assets for your business and operations.
Know which assets are on your site currently and previously, capture asset related operational costs and see a birds eye view of your operations.
Keep job sites organized, ensure assets return to the yard or are sent to the next project after another ends and control resources across operations.
Manage owned and rented assets together to stick to budget and grow your margin, account for assets to avoid loss, reduce unnecessary rental costs by better utilizing what you know you have.
Benefits
- Improved utilization/coordination of project needs
- Reduced hoarding to allocate resources appropriately and mediate disputes
- Reduced labor costs for handling and rehandling assets that a site does not need
- Improved communication and connection between teams
Superintendents can use the sites feature in their day-to-day operations to see what they have available and speed up their work.
Accountants can easily access a project’s financial information.
Equipment Managers can better manage equipment needs with visibility over each project’s asset list and make sure assets move to the appropriate locations as projects wind down.
Do you need an easy way to see the big picture from your data, and also drill down to understand segmented, meaningful chunks? We struggled with this too, and built a reporting engine to help solve the common obstacles associated with data analysis.
Equipment management systems organize your mixed asset data so you can easily see it on the platform. Export reports to get the performance insights you are looking for and benefit your Equipment Managers, Cost Accountants, Estimators and Executive team.
Benefits. With meaningful data your team can improve forecasting, decision making and communications. Accurate reporting with equipment management systems bring you increased visibility, cost earnings and savings.
Sharing and allocating resources across locations is critical to operations. It’s time to eliminate the chaos, procrastination, forgetfulness and hoarding that impacts your project needs.
Each project’s equipment requests and reservations are visible to your teams, enabling efficient communication and coordination between job sites and the equipment manager to share resources efficiently.
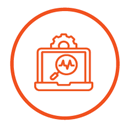
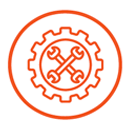
Benefits
- Improved communication between the field and the shop
- Improved coordination of project needs
- Reduced labor costs for handling and rehandling assets that a site does not need
- Improved utilization and utilization forecasting
- Reduced hoarding
Streamlining your resource management eliminates dozens of wasted hours lost by foremen, laborers, superintendents and shop personnel trying to source and obtain the right machine, tool or vehicle at the right time.
Resources Allocation lets the equipment management team coordinate operational needs with maintenance downtime, helps your teams plan ahead, reduces the need to purchase additional assets you already own and frees up your equipment to keep it working for your business.
Your equipment fleet, along with your people, generate your revenue; so equipment downtime, unexpected breakdowns and unsafe operations can have a huge impact on your top and bottom lines.
It is critical that your equipment fleet remains in good working condition for safe and optimal performance since your assets are required to build your projects. Non-working assets are extremely distruptive to productivity and budget. Equipment tracking systems make it possible for you to manage preventive maintenance and repairs to prolong your assets’ lifespans.
Know when PM services are approaching for proper planning. Be notified when repairs are requested from the jobsites, know when they are scheduled and resolved, and see full maintenance history for each asset.
Identify performance issues before they impact productivity or safety, schedule maintenance in advance to control and optimize resources, decrease impacts to projects and make more informed decisions to control operating costs.
Replace assets based on accurate R&M and cost data. Protect your capital investments, increase resale value, and spend responsibly on prevention to reduce costs on reaction with project schedules on the line.
Benefits
- Reduced emergency or unplanned maintenance issues and risks of breakdown
- Improved response times to repair requests
- Reduced operating costs and emergency repair expenses
- Improved safety and schedule efficiencies
- Improved record keeping and documentation
- Reduced mechanic labor costs and optimized time with better visibility and efficient scheduling
Field Personnel can schedule repairs directly with mechanics when required, report detailed damage or repair needs from the jobsite including photos, notes, voice memos and attachments.
Mechanics and shop personnel can see what is down for repair and for how long, easily assess repair requests from the field, see preventive maintenance schedules for each asset and view their historic service records (which help resell an asset in the future).
Do you struggle to pinpoint how your assets are used across your company? Do you run equipment into the ground deferring maintenance until a problem arises, or find yourself with a collection of the same, unused assets when closing out a job site?
We’ve been there and done that. Equipment tracking systems make it easy for you to see how your assets are being utilized across your job sites and your entire organization. This visibility lets you make more informed decisions about owning, renting, moving or selling your assets and helps make sure your assets are working for you.
Benefits. Accurate utilization data gives you better control over your assets, projects and overall business. Keep your assets working for you by staying ahead on maintenance, optimizing uptime and unloading assets no longer needed. Improved utilization yields major savings.
A key component of proper asset management and overall business success involves the safe operation of assets and regulatory compliance reporting.
Equipment tracking systems empower project, safety and administrative personnel to efficiently manage and monitor safety and compliance across your entire equipment fleet. Never get caught off guard when it comes to your equipment inspections and documentation, and address unsafe driving behaviors in time to avoid accidents or penalties.
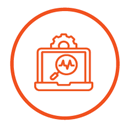
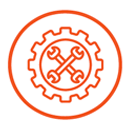
Benefits
- Reduced risk of safety incidents for improved safety performance and record
- Reduced emergency or unplanned maintenance issues and risks of breakdown
- Increased reaction and attention to insights on unsafe behaviors
- Reduced delays and execution slow downs with safer performing assets and personnel
Field Personnel can schedule repairs directly with mechanics when required, report detailed damage or repair needs from the jobsite including photos, notes, voice memos and attachments.
Mechanics and shop personnel can see what is down for repair and for how long, easily assess repair requests from the field, see preventive maintenance schedules for each asset and view their historic service records (which help resell an asset in the future).
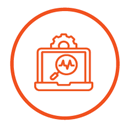
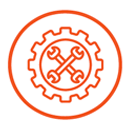
Benefits
- Increased visibility and efficiency
- Elimination of gaps in information and inaccurate reporting
- Increased time savings and reduced rework
- Increased profitability as result of gained efficiencies
- Improved productivity as result of time savings
Integrations allow different business systems to share data, communicate with each other and work together, all to help streamline your business processes.
Integrations can:
• Share data for full visibility and business intelligence
• Be built to sync automatically or based on defined triggers
• Feed specific processes and/or workflows
• Allow you to perform an action in one system from within another
• Retrieve information from various sources through APIs.